Energy Audit Checklist for Preventive Maintenance: What to Inspect and Why
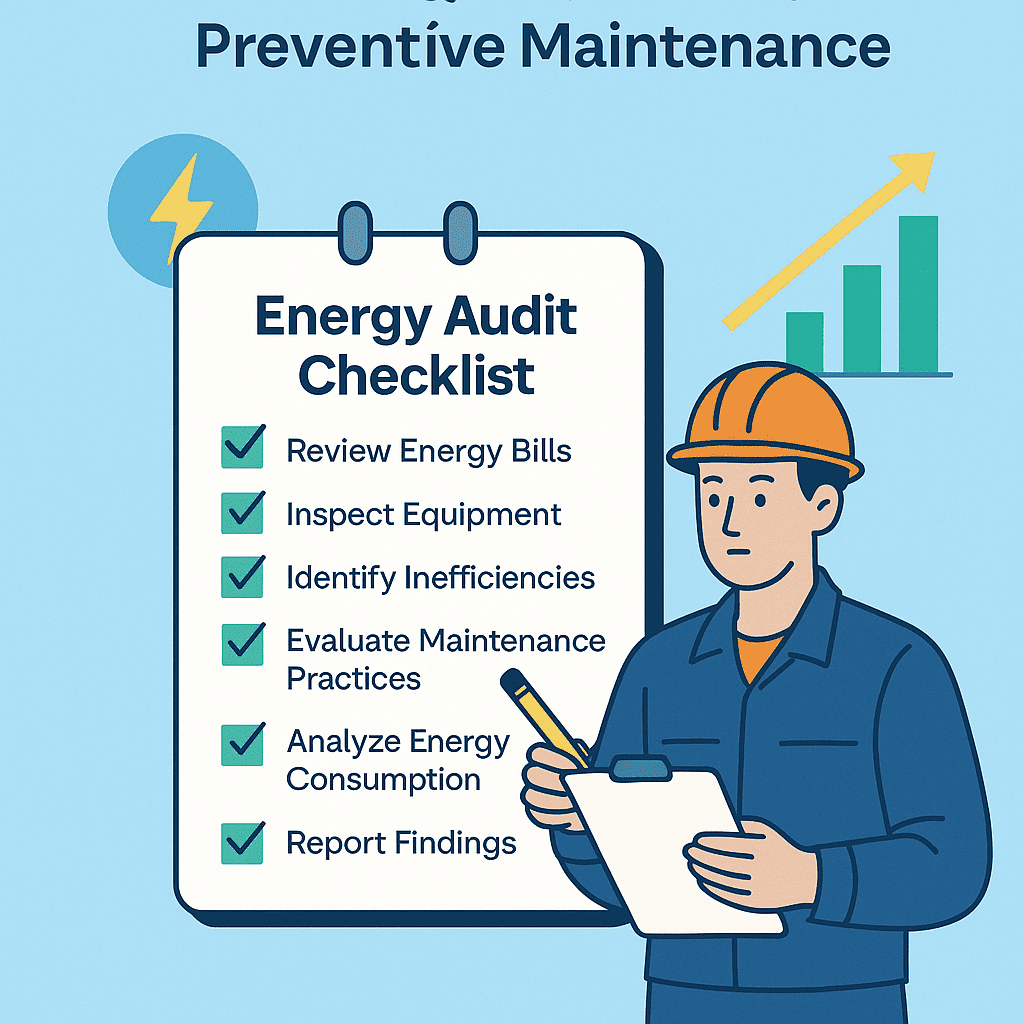
Introduction
Energy efficiency is no longer optional. With rising utility costs and growing compliance pressure, maintenance teams must go beyond routine PMs to ensure equipment isn’t silently wasting energy.
A well-structured energy audit checklist can help identify leaks, inefficiencies, and equipment issues long before they affect performance or increase your plant’s carbon footprint.
In this article, we provide a comprehensive energy audit checklist specifically tailored for preventive maintenance inspections.
1. Electrical Systems
- Inspect motor running amps vs. rated amps
- Check for unbalanced loads
- Scan for hot spots in wiring using thermal imaging
- Test for voltage drops under load
Why It Matters: Electrical inefficiencies often go unnoticed and can lead to overheating, premature failure, or excessive energy bills.
2. Compressed Air Systems
- Listen for audible leaks during off-peak hours
- Inspect drain traps and air dryer functionality
- Check pressure setpoints vs. actual operating levels
- Review air demand vs. supply capacity
Why It Matters: Leaks in compressed air systems can account for 20–30% of energy loss, making them one of the highest ROI opportunities for energy-focused PM.
3. HVAC and Chillers
- Clean filters, coils, and condensers
- Inspect refrigerant levels and pressure
- Check motor and fan alignment
- Test sensor calibration for temperature and humidity
Why It Matters: Improperly maintained HVAC units work harder than they need to, consuming excessive energy and shortening equipment life.
4. Pumps and Motors
- Check for worn impellers or motor misalignment
- Inspect vibration levels and lubrication
- Compare actual kWh usage to historical trends
- Test soft-start settings and overload protection
Why It Matters: Pump and motor inefficiency often hides in plain sight. Early detection through energy audits prevents major breakdowns.
5. Lighting and Controls
- Inspect for failed ballasts or lamps
- Confirm that occupancy or daylight sensors function properly
- Check scheduling logic for automation systems
- Identify areas for LED retrofitting
Why It Matters: Lighting audits are quick wins in energy management, especially in warehouses and large shop floors.
6. Building Envelope
- Inspect for insulation gaps around doors and windows
- Use infrared scans to detect thermal losses
- Check for air leaks in ductwork or utility penetrations
- Verify that dock doors and overheads close and seal properly
Why It Matters: Poor insulation and air leaks can undermine all other energy-saving measures by forcing systems to work harder.
How to Use This Checklist in MaintBoard
MaintBoard CMMS allows you to:
- Create reusable inspection templates with the above audit points
- Schedule recurring energy audit PMs
- Attach images, notes, and energy meter readings
- Generate audit reports by asset, zone, or category
You can even link work orders to follow-up actions triggered during audits.
FAQ: Energy Audit and Preventive Maintenance
How often should we perform an energy audit?
Ideally, once per quarter for major assets, and annually for full plant review.
Who should perform the audit?
Maintenance technicians supported by energy/facility managers.
Do we need energy meters for audits?
No, but they make the process far more effective and measurable.
Can this checklist help with ESG reporting?
Yes, it supports data collection for energy KPIs and carbon disclosure.
Conclusion: Don’t Let Energy Slip Through the Cracks
An energy audit isn’t just about compliance—it’s about control. By integrating a preventive energy checklist into your maintenance strategy, you reduce waste, prolong asset life, and position your facility as a leader in operational efficiency.
MaintBoard makes it easy to digitize, automate, and act on your audit findings.
Book a demo or talk to our team to learn how.