Essential Bowling Lane Downtime Prevention: 7 Causes and How to Avoid Them
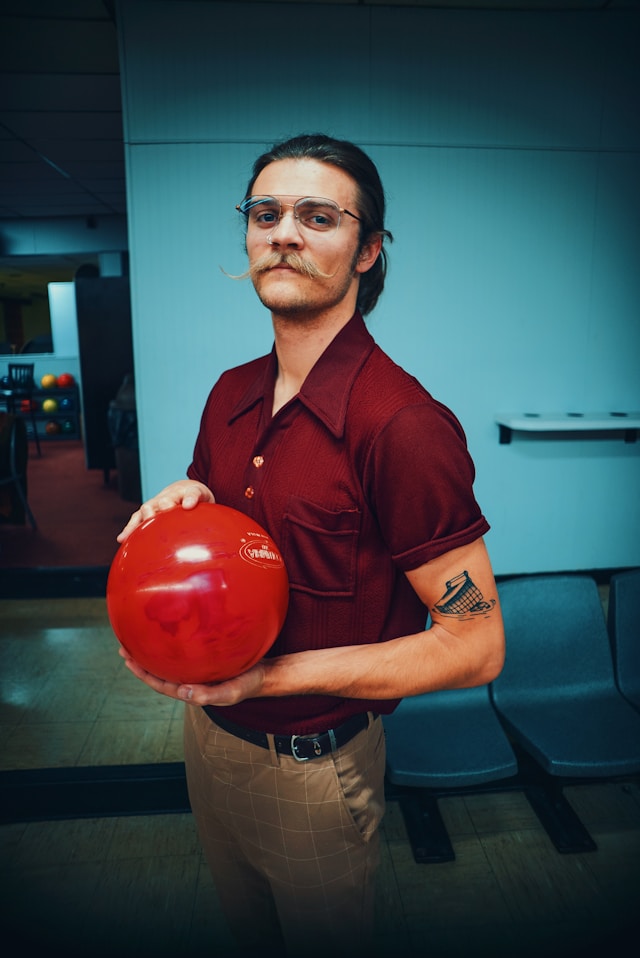
Bowling lane downtime prevention isnβt just about avoiding delays β itβs about protecting revenue, improving bowler satisfaction, and extending the life of your most valuable equipment.
Whether you run a small local center or manage dozens of lanes, the key to reducing lane downtime lies in identifying root causes and addressing them with proactive systems. Below are the top 7 causes of bowling lane downtime β and the steps you can take to avoid them.
1. π§ Pinsetter Jams
π The #1 cause of sudden lane stoppage and unhappy bowlers.
Why it happens:
Loose hardware, pit debris, misaligned sweep arms, or worn clutches.
How to prevent it:
β
Clean the pit daily
β
Check alignment and lubricate moving parts weekly
β
Inspect motors and clutches monthly using a CMMS checklist
2. π³ Ball Return Malfunctions
Why it happens:
Worn or broken belts, dirty tracks, or misaligned return paths.
How to prevent it:
β
Inspect ball return systems weekly
β
Clear dust, rubber debris, and spilled drinks
β
Replace belts before they snap β not after
3. β‘ Electrical & Sensor Failures
Why it happens:
Aging wiring, loose sensor connections, or unprotected power surges.
How to prevent it:
β
Test sensors monthly (especially on older scoring systems)
β
Use surge protectors on sensitive electronics
β
Track repeat sensor failures by lane using a CMMS
4. π€οΈ Lane Surface Damage
Why it happens:
Dropped balls, skipped oiling cycles, or harsh cleaning chemicals.
How to prevent it:
β
Train staff to handle balls properly
β
Wipe lanes daily and follow a strict oiling schedule
β
Use only approved cleaning products
5. ποΈ Missed Preventive Maintenance
Why it happens:
No checklist, no ownership, and no system in place.
How to prevent it:
β
Use a CMMS (like MaintBoard) to assign and track recurring PM tasks
β
Attach checklists by zone (pinsetters, lanes, arcade, etc.)
β
Hold staff accountable with clear due dates
6. π Lane Oiling Machine Errors
Why it happens:
Improper calibration or skipped cleaning routines.
How to prevent it:
β
Clean oiling machines weekly
β
Monitor application patterns to avoid lane inconsistencies
β
Compare output to pattern specs and adjust regularly
7. π Operator Errors
Why it happens:
Undertrained staff, rushed resets, or misuse of emergency stop features.
How to prevent it:
β
Train all staff on emergency resets and common issues
β
Keep laminated quick-reference guides at each lane
β
Limit access to mechanical areas for untrained employees
π§ Why Bowling Lane Downtime Prevention Pays Off
Lane downtime affects your peak hour profits more than you think. A single failure during a birthday party or league night can cause backups, refunds, or negative reviews.
The solution? Pattern recognition and structured scheduling.
- Track issues by lane
- Set recurring tasks with checklists
- Assign ownership through a CMMS like MaintBoard
Centers that implement this approach see 30β40% fewer breakdowns over time.
π Bowling Lane Downtime Prevention Summary
Issue | Prevention Strategy |
---|---|
Pinsetter Jams | Daily pit cleanups, weekly alignment, monthly checks |
Ball Return Failures | Weekly inspection, debris removal, belt replacement |
Electrical / Sensor Issues | Monthly testing, surge protection, track failures |
Lane Surface Damage | Daily wipes, oiling, staff training |
Missed PM Tasks | CMMS with reminders and role-based tasking |
Oiling Machine Errors | Weekly cleaning, verify oil patterns |
Operator Mistakes | Staff training, reset guides, controlled access |
π Frequently Asked Questions
What lane issues cost the most to fix?
Pinsetter motor replacement and scoring system failures are among the most expensive. Most can be prevented with basic monthly checks.
Is one lane more likely to fail than others?
Yes β lanes used for parties or league play tend to wear faster. Track by lane to adjust your service frequency.
Can I monitor and log breakdowns digitally?
Absolutely. MaintBoard lets you log downtime by lane, assign PM tasks, and track recurring issues over time.
π‘ Final Tip: Build a Bowling Lane Downtime Prevention Mindset
Every failure leaves clues β if youβre looking for them.
By staying ahead of these 7 common causes and using a CMMS like MaintBoard, you can dramatically reduce unplanned lane closures and protect your weekend revenue.
π Stay on schedule. Track what breaks. Prevent issues before they impact your bowlers.