Essential Bowling Alley Maintenance Checklist for Smoother Operations
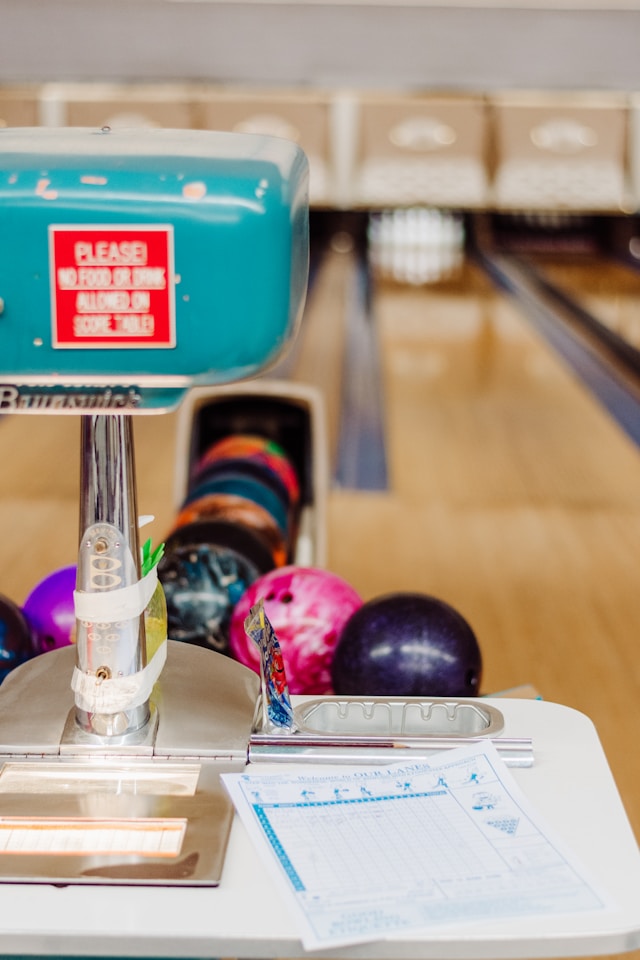
Running a bowling center means managing more than just shiny lanes and ball returns — it’s about keeping every part of your facility reliable, clean, and safe. Whether you operate 8 lanes or 48, a structured bowling alley maintenance checklist ensures that small issues don’t turn into big, expensive problems.
This guide walks you through all the essential checks — broken down into five main zones of your facility — so your team can stay ahead of equipment failure and maintain the customer experience.
🎯 Why a Maintenance Checklist Matters for Bowling Centers
Without a checklist, teams often react to problems instead of preventing them. A missed HVAC filter change, skipped pinsetter lubrication, or forgotten freezer coil cleaning can lead to:
- Lane closures on busy nights
- Disappointed league bowlers
- Food and beverage delays
- Emergency repair costs
A digital bowling alley maintenance checklist ensures every part of your operation is checked on time — no guesswork, no gaps.
🧱 Bowling Alley Maintenance Checklist (By Zone)
🏟️ Facility Equipment Maintenance
- HVAC Systems — Clean filters monthly, check airflow and thermostat accuracy
- Lighting Fixtures — Inspect bulbs, ballasts, and emergency lighting every 30 days
- Fire Extinguishers / Safety Systems — Verify placement and expiration dates quarterly
🎳 Core Bowling Equipment Maintenance
- Pinsetters — Daily, weekly, and monthly routines (see our pinsetter guide)
- Ball Return Systems — Check for belt wear, motor vibration, and jams weekly
- Lanes — Wipe daily, oil weekly, inspect surface wear monthly
- Pin Decks / Gutter Guards — Confirm alignment and tighten parts monthly
🍕 Food & Beverage Equipment
- Refrigerators / Freezers — Check temps daily, clean coils monthly
- Ovens / Fryers — Inspect filters and ventilation weekly
- Soda Dispensers / Beer Taps — Clean weekly and test flow daily
🕹️ Arcade & POS Systems
- Game Machines — Monthly inspection of wiring, screens, and buttons
- POS Terminals — Run updates, clean hardware bi-weekly
- Redemption Counters — Ensure printer and sensor functionality
📅 Admin & PM Scheduling Tools
- Weekly / Monthly Matrix — Assign rotating tasks to team members
- Use a CMMS like MaintBoard — Automate PM schedules, get reminders, and log work history
🔧 How to Implement This Checklist
Start small and build consistency:
- Break down your center into zones (as shown above)
- Assign responsibilities — daily checks to openers, weekly to techs
- Digitize your checklist using MaintBoard or another CMMS
📍 Example: A 16-lane center might do HVAC and arcade on Monday, pinsetters on Wednesday, and kitchen on Friday.
📋 Real-World Example: What a Weekly Maintenance Routine Looks Like
To give you a head start, here’s what a simple weekly plan might include for a 16-lane center:
- Monday: Clean HVAC filters, inspect arcade systems
- Wednesday: Run oiling machine and inspect all pinsetters
- Friday: Check fire extinguishers, restock POS supplies
- Sunday: Clean kitchen ventilation filters
This cadence ensures your tasks are spread out, and no area is neglected.
🧠 Mini Case Study: How One Center Reduced Breakdowns by 40%
One 12-lane center in the Midwest started using MaintBoard to schedule all weekly PMs across five zones. After three months:
- Pinsetter downtime dropped by 40%
- Techs completed 92% of assigned tasks on time
- Customer complaints related to arcade machines fell to zero
👉 All of this happened just by using checklists, tracking completion, and assigning responsibility.
⚠️ Common Mistakes to Avoid
- Skipping HVAC filter changes until airflow fails
- Ignoring arcade or POS issues until customers complain
- Using paper logs that no one checks
- Not assigning ownership to a team member
🙋 Frequently Asked Questions
What’s the best way to manage recurring tasks?
Use a CMMS like MaintBoard — it auto-schedules, sends reminders, and stores task completion logs.
Is this checklist useful for small centers too?
Yes. With fewer lanes, each breakdown has more impact. PM matters more, not less.
Can I skip areas I don’t use often?
You can, but regular checks catch small issues before they grow. Even low-use equipment breaks down when ignored.
How often should I update my bowling alley maintenance checklist?
At least once per quarter. Update it whenever you add new equipment, change operating hours, or notice patterns in equipment failures.
What’s the best way to train staff on using the checklist?
Start with a walkthrough during a team meeting, pair new hires with a tech for shadowing, and post laminated copies in key areas. A CMMS like MaintBoard makes it even easier with mobile access and digital tracking.
🚀 Final Tip: Start Small, Stay Consistent
This bowling alley maintenance checklist is your foundation for better operations. Use it to assign tasks, avoid downtime, and improve team accountability — no matter your facility size.
👉 Want to make this even easier? Use MaintBoard to digitize this checklist and automate your weekly PM schedule.