GMP Equipment Maintenance Checklist: 7 Proven Steps to Stay Audit-Ready
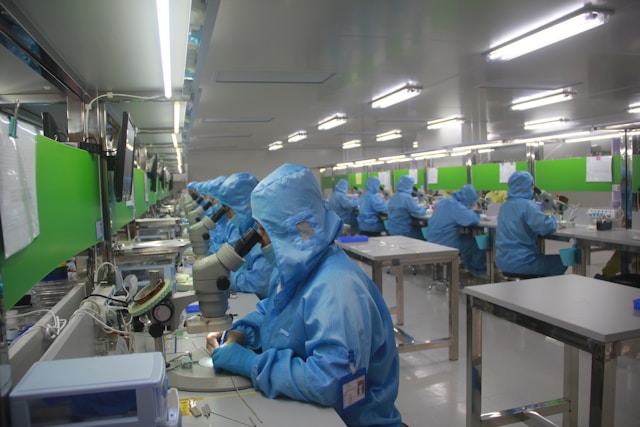
Introduction: GMP Equipment Maintenance Checklist That Actually Works
If you’re working in a pharmaceutical facility, following a GMP equipment maintenance checklist isn’t just a best practice — it’s a regulatory must.
Maintaining pharmaceutical equipment under GMP isn’t optional — it’s the foundation of reliable production. This checklist will walk you through the critical steps that help reduce risk, improve efficiency, and show auditors that your systems are fully under control.
Whether you’re managing production lines, packaging units, or cold rooms, equipment failures can lead to contamination, rejected batches, and even halted operations. Auditors from the FDA, WHO, or EMA expect proof that preventive maintenance is performed regularly, thoroughly, and with full traceability.
In this article, you’ll get a 7-step GMP equipment maintenance checklist that your QA and maintenance teams can follow to ensure compliance, reduce downtime, and pass audits with confidence.
Why GMP Equipment Maintenance Matters
- ✅ Ensures consistent product quality and safety
- ✅ Prevents unplanned downtime and equipment failure
- ✅ Satisfies regulatory expectations for documented maintenance
- ✅ Builds trust and credibility during GMP audits
Neglecting equipment maintenance in GMP environments leads to unnecessary risks — both operationally and regulatory.
🧰 Daily GMP Equipment Maintenance Checklist
Task | Equipment Type | Why It’s Important |
---|---|---|
Record equipment status | Production lines, cold rooms | Detect early warning signs |
Check temperature/humidity | Cold storage, cleanrooms | Maintain environmental integrity |
Visual inspection for leaks/vibration | Pumps, compressors, HVAC | Prevent serious failures |
Ensure cleaning SOPs are followed | Fillers, mixers, packaging | Prevent contamination |
📅 Weekly GMP Maintenance Checklist
Task | Equipment Type | Purpose |
---|---|---|
Inspect seals and hinges | Isolators, cold rooms | Maintain air tightness |
Check belts, filters, motors | Freezers, HVAC units | Ensure efficiency and airflow |
Verify alarms and sensors | Monitoring equipment | Confirm alert functionality |
Clean coils and vents | Refrigerators, chillers | Improve energy efficiency |
🗓️ Monthly GMP Maintenance Tasks
Task | Equipment Type | Purpose |
---|---|---|
Calibrate probes/sensors | Temp and humidity devices | Ensure accurate readings |
Review and archive PM logs | All assets | Guarantee traceability |
Test backup systems | UPS, generators | Prepare for power loss |
Conduct OQ spot checks | Critical equipment | Confirm operational reliability |
📁 Documentation & GMP Compliance Tips
- Use digital PM forms via CMMS with timestamps and technician signatures
- Maintain calibration certificates and SOPs in one central system
- Document deviations with root cause and corrective action
- Always version-control your maintenance SOPs
✅ Use a CMMS to Automate GMP Maintenance
A CMMS (Computerized Maintenance Management System) simplifies GMP compliance by:
- Scheduling and assigning maintenance by frequency and asset
- Tracking every maintenance activity with technician accountability
- Linking calibration records and SOPs to each equipment entry
- Generating instant, audit-ready reports for regulatory inspections
- Reducing manual errors and missed tasks
MaintBoard CMMS is purpose-built to help pharma teams meet GMP standards effortlessly — and stay inspection-ready every day.
Many pharmaceutical companies are moving from paper-based logs to digital CMMS platforms to improve traceability, reduce manual error, and prepare faster for regulatory inspections.
Frequently Asked Questions
Is a maintenance SOP required for GMP?
Yes. Every GMP-compliant facility must have maintenance SOPs that define frequency, responsibility, and documentation procedures.
Can I use Excel sheets for GMP logs?
Technically yes, but spreadsheets don’t meet traceability requirements. A CMMS provides timestamped, role-based digital logs preferred by auditors.
What if we miss a scheduled maintenance task?
Log it as a deviation, perform root cause analysis, and apply corrective actions. Frequent misses without documentation raise audit flags.
How often should GMP equipment be calibrated?
Calibration frequency depends on the equipment type and its criticality to product quality. However, most GMP facilities calibrate sensors, probes, and measuring devices at least monthly or quarterly, with records stored for audit readiness.
What documentation is required for GMP equipment maintenance?
You need maintenance logs with timestamps, technician initials, calibration certificates, deviation records, SOPs, and equipment qualification reports (IQ, OQ, PQ). These must be traceable and version-controlled.
Can I use a CMMS to track calibration schedules too?
Yes. A CMMS can schedule and document calibration tasks, store certificates, and trigger alerts for overdue equipment — making it easier to meet GMP expectations.
Conclusion: Stay Compliant, Stay Ahead
Following a solid GMP equipment maintenance checklist isn’t just good practice — it’s key to keeping your facility compliant, safe, and efficient.
Whether you’re preparing for your next audit or building a stronger maintenance culture, this 7-step checklist and a smart CMMS like MaintBoard can help you scale with confidence.
👉 Download our GMP Equipment Maintenance Checklist (coming soon) or Book a Free CMMS Demo with MaintBoard today.